« Cette excellente vulgarisation de la corrosion des spits précise pour la première fois l’origine de certaines anomalies qui étaient alors classées jusque-là comme de la CSC. »
— Carmela Malomo
Ingénieur, présidente de Daidalea, association d’équipeurs d’Italie
Depuis 2010, et même avant, on sait que les spits en inox 316L peuvent subir divers types de corrosion, ce qui provoque une diminution de leur résistance. C’est le cas notamment de la corrosion sous contrainte (CSC). De leur côté, fabricants, UIAA et autres organismes répètent que la CSC est à l’origine de nombreux défauts1. À la même époque, des équipeurs ont attiré l’attention sur d’autres causes possibles que celle qui faisait l’unanimité, en vain. De récentes analyses de laboratoire établissent désormais l’origine d’une bonne partie des problèmes de l’inox : sa qualité n’est pas toujours celle qui est indiquée, ou différents matériaux ont été mélangés (contrairement aux règles de l’art) ou encore la soudure des anneaux a été mal exécutée, voire plusieurs de ces anomalies sont cumulées ! Et de tels défauts sont toujours actuels !
Les problèmes
En principe, un spit (une plaquette et un tampon ou goujon), une broche, un anneau, une boucle ou une chaîne, supporte une charge d’environ deux tonnes, pour autant que le rocher soit sain, et c’est pourquoi ce type d’équipement a été privilégié. C’est le cas de ceux en inox A4 316L, qui sont les plus utilisés2 ces dernières années. Pourtant, de nombreux spits ont présenté de graves anomalies : pièces défectueuses, mauvaise soudure, en particulier, avec pour conséquence que le matériel rouille rapidement puis casse, parfois même sans devoir supporter la chute d’un grimpeur ni même son poids ! Le but de cette contribution n’est pas de jeter la pierre sur tel ou tel fabricant (c’est pourquoi ils ne sont pas nommés) mais de faire prendre conscience du phénomène afin d’améliorer la sécurité en particulier avec l’équipement en bord de mer. Même si ce risque est moins marqué sur le continent, soyez vigilants dans le choix du matériel et sur le terrain observez ce qui est en place. En cas de doute, dû par exemple à de la rouille sur de l’inox, prenez vos dispositions et annoncez le cas (voir plus loin).
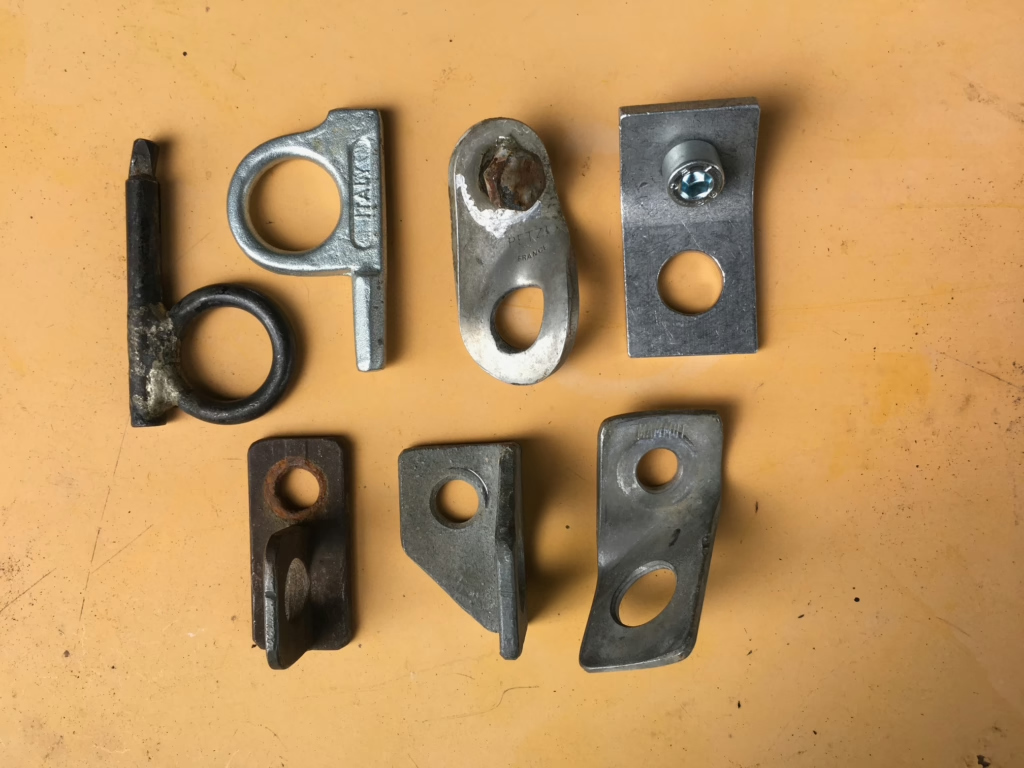
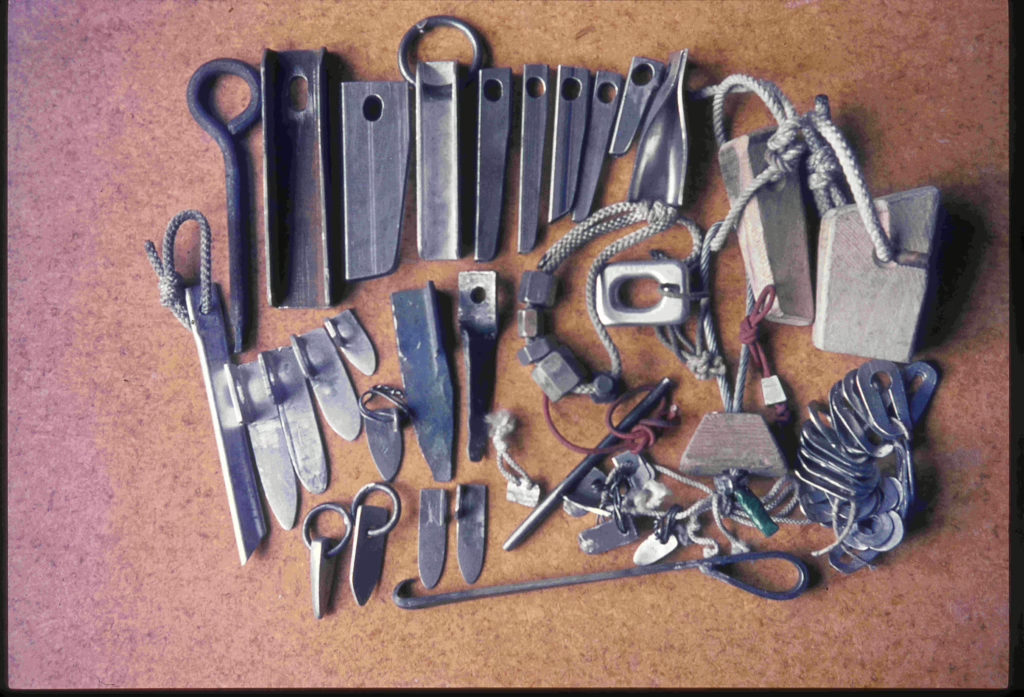
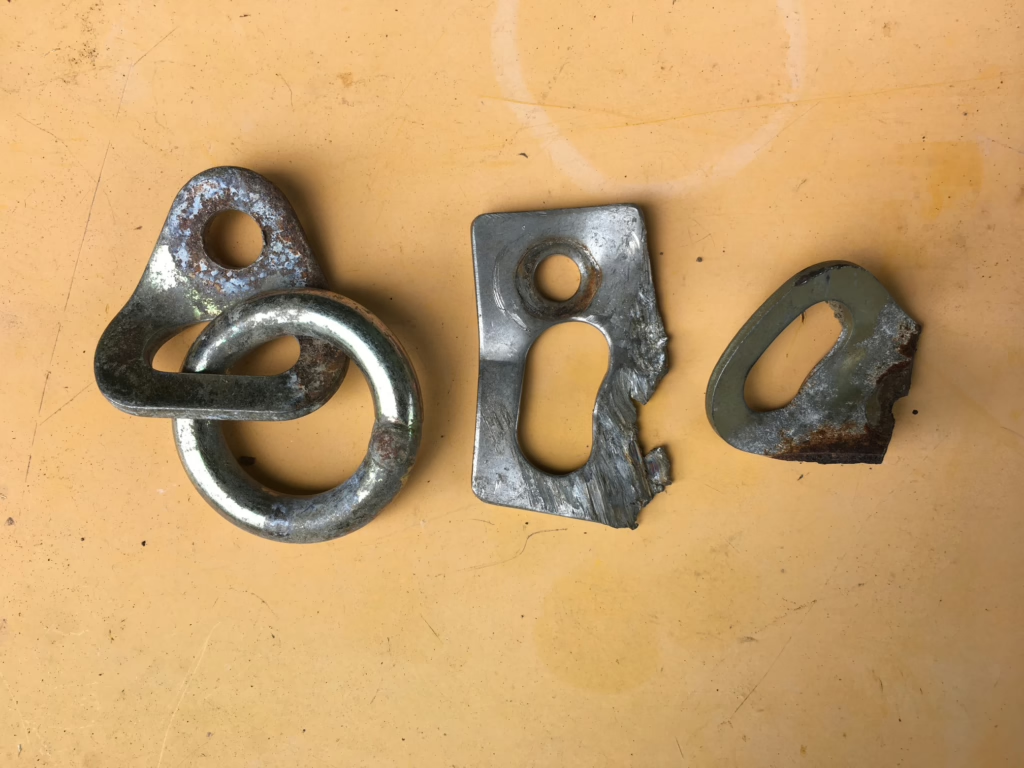
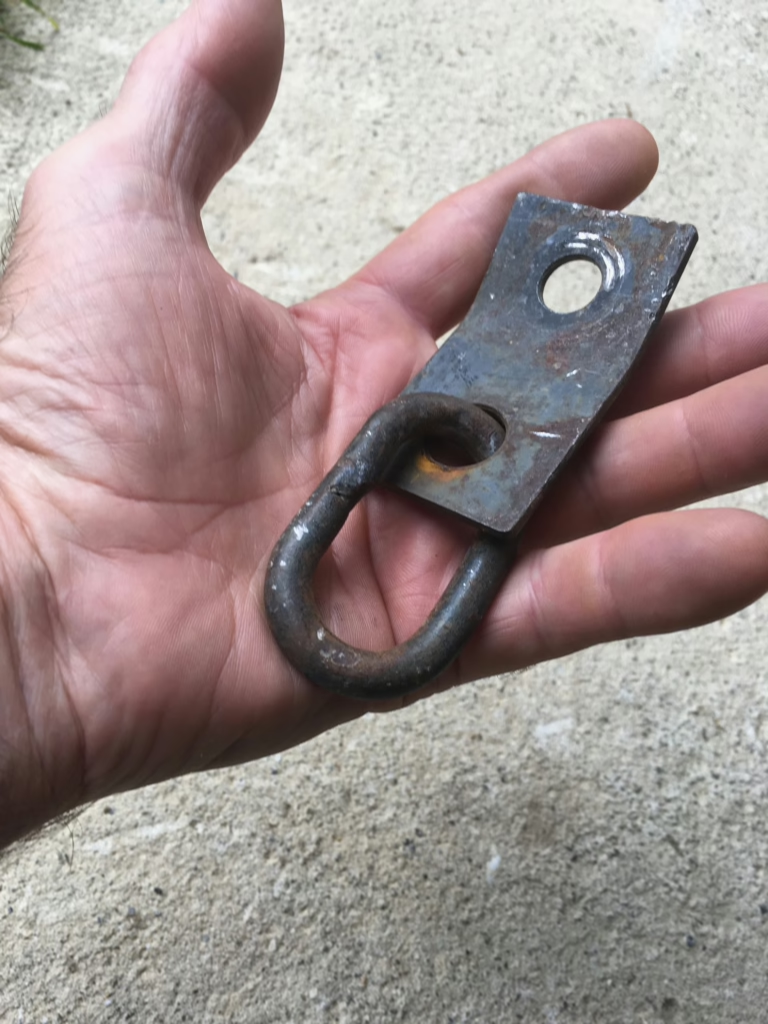
Des normes non respectées !
Diverses normes, comme celles de l’Union Internationale des Associations Alpines (UIAA), sont utilisées par les fabricants de matériel d’alpinisme et d’escalade comme références techniques et arguments de vente. De la sorte, les cordes, les baudriers et les mousquetons sont des produits reconnus pour leur solidité et leur fiabilité, et à juste titre. Malheureusement, certaines pièces, une fois fixées sur le rocher révèlent de sérieuses défectuosités, qui sont le plus souvent imputables à des fabricants pourtant spécialisés, qui se prévalent du respect des normes en la matière. Ce qui surprend, c’est non seulement l’ampleur des problèmes mais aussi le fait qu’ils se répètent régulièrement au fil du temps. Pourtant, les matériaux, les techniques de fabrication et les protocoles de contrôle sont parfaitement connus et maîtrisés depuis fort longtemps. Que ce soit dans l’industrie, dans la médecine, dans les tunnels ou dans la construction navale, on utilise avec succès l’inox A4 316L y compris dans des environnements salins humides ou pollués. Même dans des rudes conditions cet inox résiste aux sollicitations et au temps, ce qui devrait exclure tout problème de qualité du matériel d’escalade. Hélas ce n’est pas le cas.
L’évolution du matériel
Avant d’en venir aux défauts rencontrés, il semble utile de rappeler l’évolution de cet équipement. Après les premiers petits pitons à compression ou à expansion, d’abord pour l’escalade artificielle,puis les gollots (spits) artisanaux ou industriels, on en est venu, dans les années 60-70, aux tampons tels que les Phillips ou les Tilca, généralement de diamètre M8 en acier. On y vissait des plaquettes bricolées, ou vrillées, comme celles de Petzl en anticorodal pour la spéléo, mais qui étaient également employées pour équiper des voies. On les utilisait avec parcimonie car les trous étaient alors forés à la main à l’aide d’un tamponnoir. Dans les années 80, on est progressivement passé au diamètre M10 avec écrou et des plaquettes spécifiques à l’escalade. Désormais, on trouve sur le marché cet équipement en acier3 ou en inox4 ainsi que des boucles (anneaux) pour les relais. Dès 1985, la pose de ce matériel a été considérablement facilitée par la perceuse à accus. Elle a entraîné une multiplication des itinéraires et une augmentation du nombre de points fixés par longueur. Le spit M10 avec écrou est devenu le plus usuel5. Il a également été employé dans des régions où son usage était peu courant, par exemple en bord de mer, où il s’oxyde rapidement à cause de l’air salin. Pour y remédier, de l’inox A2 a été utilisé comme référence, ce qui surprend car sa composition est connue pour ne pas résister à la corrosion dans ce milieu. Vers 2010, l’inox A4 316L, résistant à la corrosion marine, est devenu la norme pour équiper presque partout, sauf des régions très chargées d’air salin humide (Thaïlande) de pollution ou de sulfure (régions volcaniques).
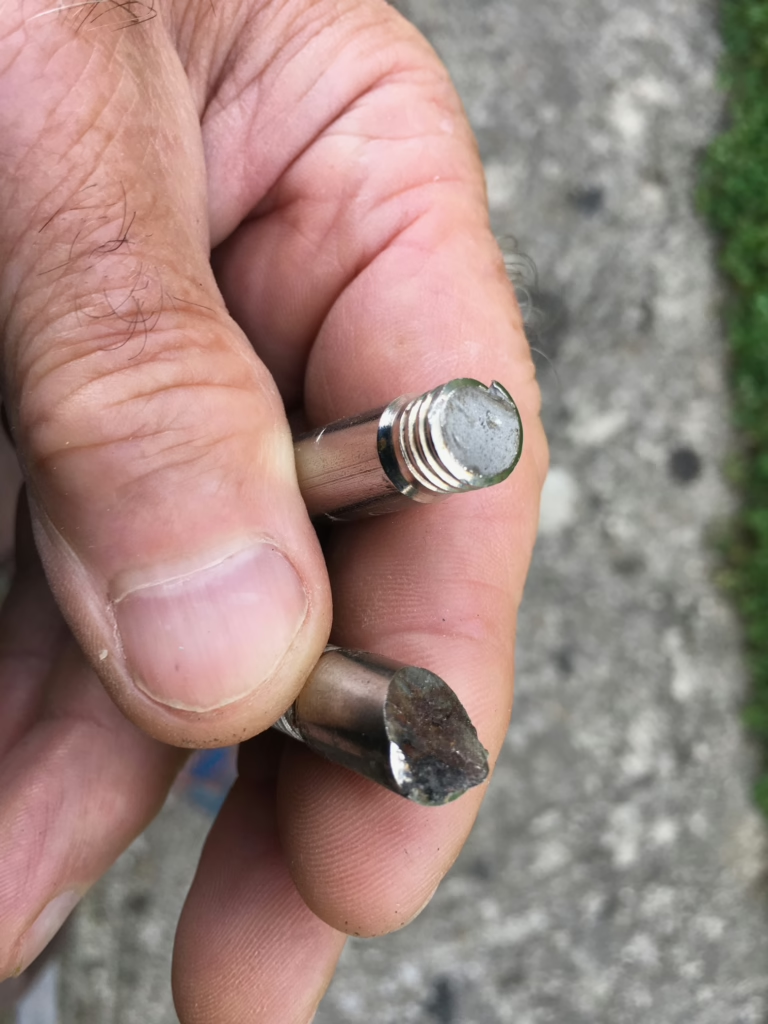
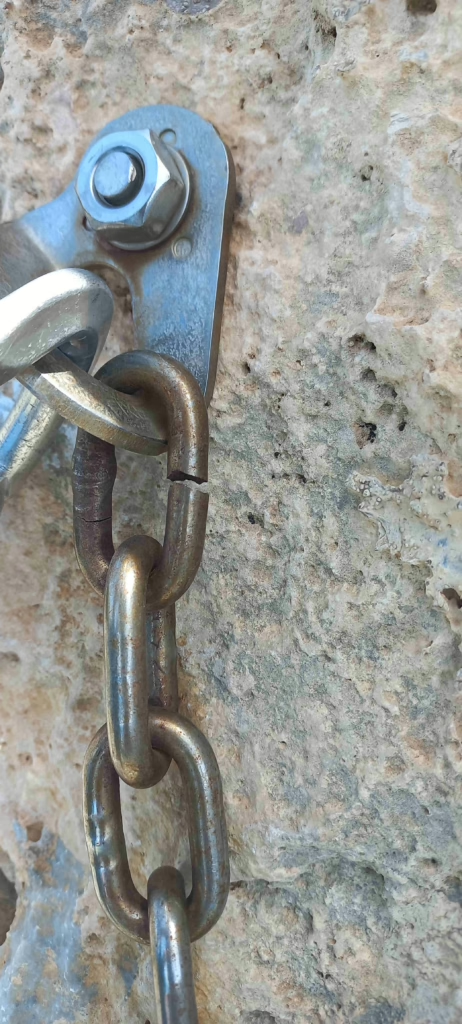
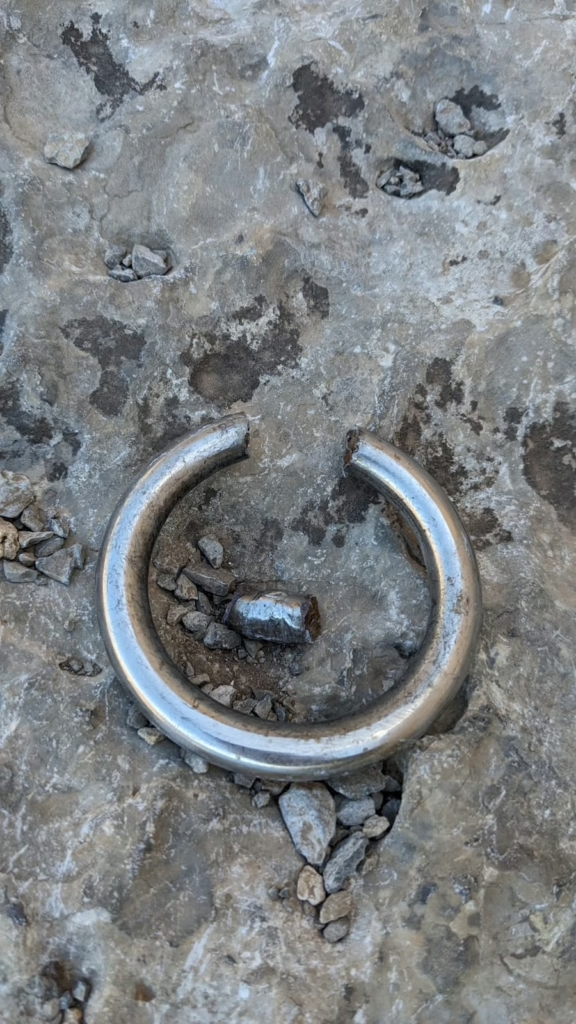
Les défectuosités rencontrées
Au fil des années, des différences de comportement des spits ont été observées. Assez tôt, certains équipeurs ont compris que c’était dû à un problème de qualité de l’inox. Mais les fabricants, l’UIAA et d’autres organismes ont toujours asséné que la corrosion sous contrainte, la CSC (l’anglais est plus précis : stress corrosion cracking = SCC) est le principal problème en présence d’air salin humide ou pollué, même pour des produits conformes et convenablement installés. Et leur opinion n’a pas varié, même aujourd’hui, alors qu’on savait depuis 2010, sans preuve absolue, que la CSC n’est pas l’unique cause des problèmes. En effet, la plupart des défauts trouvent leur source en amont : ils sont liés à l’utilisation d’un autre inox que celui indiqué ou à des boucles mal soudées, ou encore à l’assemblage de différents matériaux pour les diverses pièces du même spit (mélangé par des fabricants eux-mêmes, ce qu’ils recommandent pourtant de ne pas faire tout comme l’UIAA), ce qui entraîne une corrosion galvanique6. Le plus souvent, ce n’est donc pas une CSC (ce qui est vague), qui est à l’origine de l’affaiblissement du matériel, mais une autre anomalie que l’on peut souvent préciser comme le relève des équipeurs, par exemple : des boucles ou des chaînes en acier sont soudées sur des plaquettes inox A4 316L, ce qui arrive encore actuellement !
Voici brièvement quelques cas connus parmi de nombreux autres. Avant 2008, le soussigné et plusieurs grimpeurs ont constaté à Kalymnos, en Grèce, que des spits cassaient très occasionnellement. Il s’agissait alors de spits de diamètre M8 voire M10, en simple acier. Mais en automne 2011, dans la voie Reize à North Cape, qui pourtant venait d’être équipée, un tampon neuf M10 en inox s’est brisé alors que Renée Guerin, assurée par Bruno Fara7, se tirait simplement à une dégaine. À la même période sur cette île, dans une autre nouvelle voie équipée de matériel neuf, alors qu’un Anglais se reposait sur un spit, celui-ci a cassé, de même que le suivant lors de la chute qui s’en est suivie8 ! Il est alors apparu que c’était un fabricant grec de l’époque qui avait fourni, pendant deux ans, un équipement non conforme aux équipeurs de Kalymnos. Peu après, tout ce matériel douteux a été remplacé.
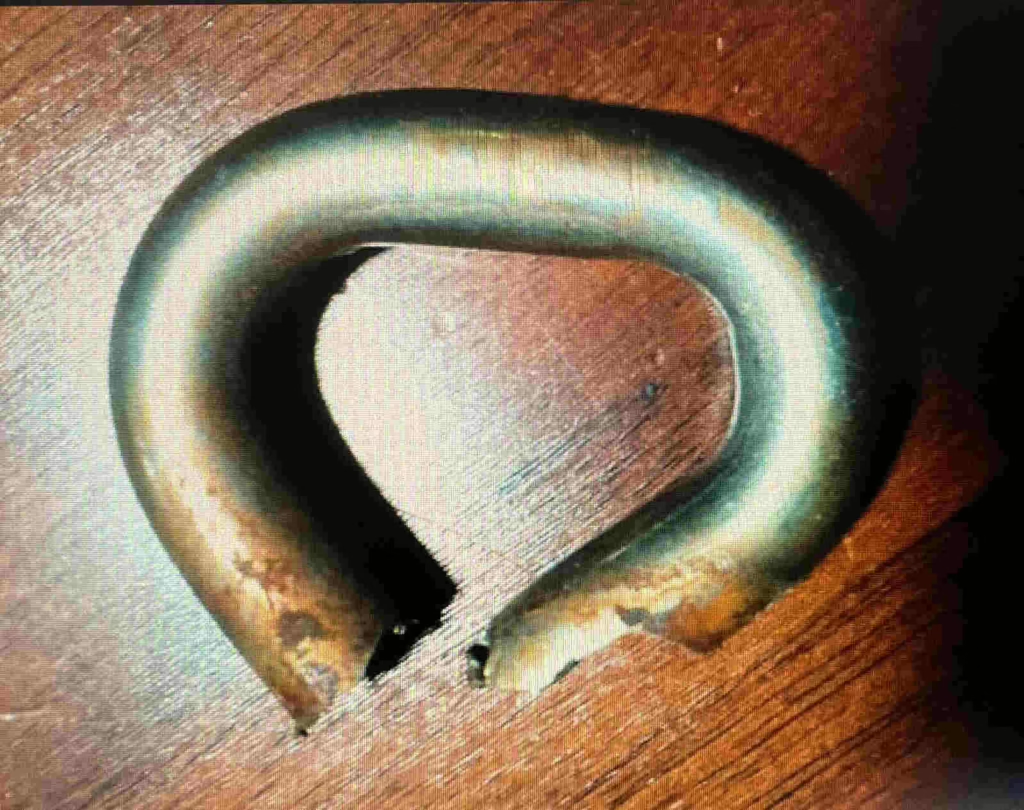
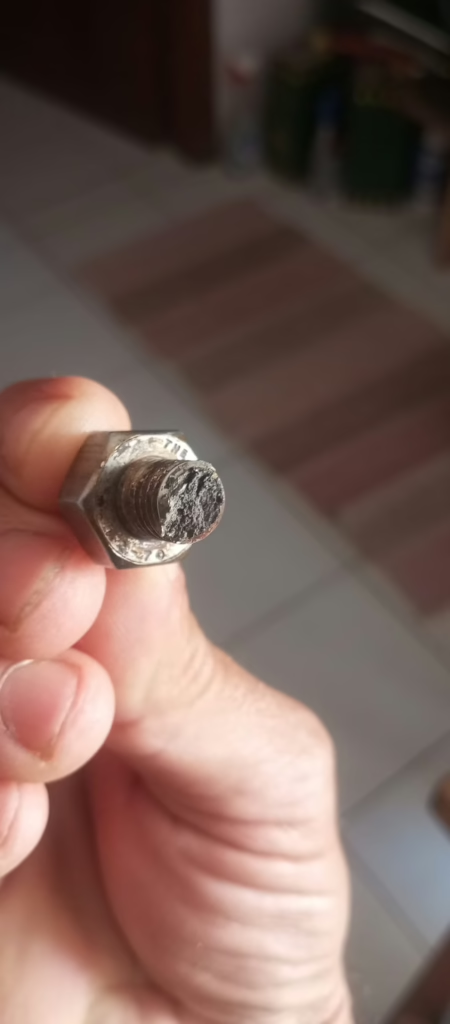
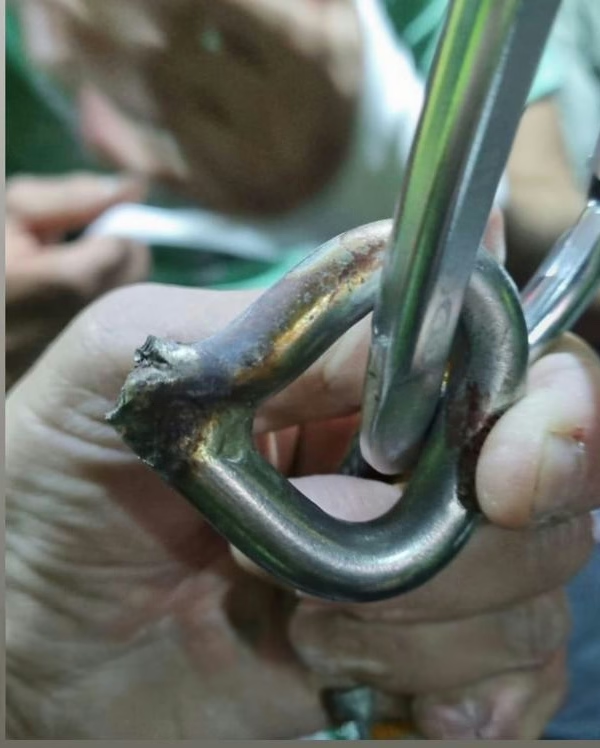
A la même époque, plusieurs équipeurs ont constaté qu’un tampon d’une marque pourtant réputée et aux normes UIAA, était affecté d’un défaut récurrent : environ un sur dix tournait dans le vide lors du serrage.
En 2014, en bord de mer dans la région de Sperlonga, Italie, où se trouve la Grotta dell’Arenauta, Federico D’Isep, Enrico Mazzoli et d’autres grimpeurs ont aussi constaté, parfois lors de terribles frayeurs, que des spits et des chaînes de marques connues cassaient facilement, comme à Kalymnos ! Il a fallu du temps pour comprendre : ce n’était ni le sulfure, ni l’air marin, ni une mauvaise fixation, ni du mauvais rocher, comme on l’avait d’abord cru – ou comme certains l’ont fait croire – mais de l’inox qui n’était pas de la qualité adéquate à environnement marin. Ce qui a été démontré par des analyses effectuées plus tard, sur du matériel endommagé qui avait été conservé, par le Professeur Ulderico Santamaria, directeur du Laboratoire de diagnostic et science des matériaux « Michele Cordaro » de l’Université Tuscia de Viterbo, en Italie. Soulignons que de tels problèmes ont été rencontrés avec de nombreux spits essentiellement en bord de mer dans plusieurs pays. Et la liste de ces anomalies n’a fait que s’allonger.
Par contre, à San Vito lo Capo, en Sicile, malgré la présence de sulfure et d’embruns humides et salins provenant de forts vents d’ouest, Daniele Arena, qui suit attentivement la corrosion des spits, n’a constaté aucune attaque sur l’inox posé dans les années 80, ni sur ceux en inox A4 316L utilisés pour les rééquipements. Cela peut s’expliquer par le fait que des zones sont naturellement protégées par exemple par des vents d’ouest ou que le sel présent sur les lieux est « lavé » par les pluies, mais aussi par la bonne qualité de l’inox.
Il y a quelques années, différents fabricants ont vanté un nouveau spit en inox PLX. Mais après le serrage de l’écrou au tampon, il n’était plus possible de le dévisser pour changer la plaquette. De plus, bon nombre de ces spits ne pouvaient être mis en place correctement. Il fallait repercer pour en fixer un autre, ce qui démontre le peu de tests et de contrôles effectués avant la mise en vente de ce matériel pourtant indiqué comme étant fabriqué selon les normes pour l’escalade. Là encore, les spécificités de ce PLX étaient pourtant connues pour d’autres emplois.
Comme déjà évoqué précédemment, des équipeurs, dont des spécialistes de plusieurs pays, découvrent régulièrement que des tampons se fixent mal dans la roche : il est alors impossible de les serrer correctement car ils tournent dans le vide, ou ils ressortent de la moitié de leur logement. Il faut alors repercer et placer un autre tampon. Dans ce cas, il est difficile de définir si c’est une anomalie liée au rocher ou à un défaut du tampon ou encore une mauvaise pose de l’équipeur, mais il est curieux de constater que ce problème est récurrent chez certains fabricants alors qu’il ne l’est pas chez d’autres. Précisons sur ce point que les validations en laboratoire devraient être complétées par la qualification des procédés industriels chez le fabricant et par des véritables tests d’emploi sur le terrain.
Le 23 février 2024, une photo sur le net (photo 001) présente une boucle de relais fendue, pourtant présentée comme étant en inox A4 316L dans le respect des normes UIAA. Ce matériel avait été posé neuf en 2022, à Leonidio, en Grèce. Après vérification sur place, la municipalité et le constructeur ont été informés par le soussigné que toutes les boucles récentes de cette marque, selon des observations effectuées sur de nombreuses voies de plusieurs secteurs (la liste des voies a été donnée aux deux mentionnés), présentaient de la rouille au niveau de la soudure et que bon nombre étaient fissurées voire fendues (photos 002-005) ! Précisons que les boucles d’autres entreprises, situées à proximité, ne montraient pas ce type de défaut alors qu’elles avaient été posées plusieurs années auparavant (dont certaines au bord de mer). Début avril 2024, le fabricant concerné est venu à Leonidio présenter un dossier9 qui détaille les origines des problèmes de corrosion, dont la CSC, le sulfure ou une mauvaise pose. Il a bien fallu admettre que ces deux dernières causes possibles étaient exclues (concernant le sulfure le rocher avait été analysé). Dès lors, pour le constructeur, il s’agissait nécessairement de CSC. Pourtant, la rouille caractéristique le long de la soudure indique un travail mal fait ou un métal non conforme, voire les deux. À l’évidence, dans ce cas comme dans d’autres, la CSC est invoquée à tort pour tenter de justifier ce qui constitue en réalité un évident défaut de fabrication qui est bien démontré par des boucles fissurées ou fendues ! Plus encore, peu après, des analyses faites par le laboratoire du Professeur Santamaria, ont établi que les soudures, les boucles et les plaquettes de ce fabricant n’étaient pas de la qualité annoncée10 ! Précisons que ce Professeur est habilité en Italie à exécuter des analyses qui ont valeur de preuve pour les tribunaux.
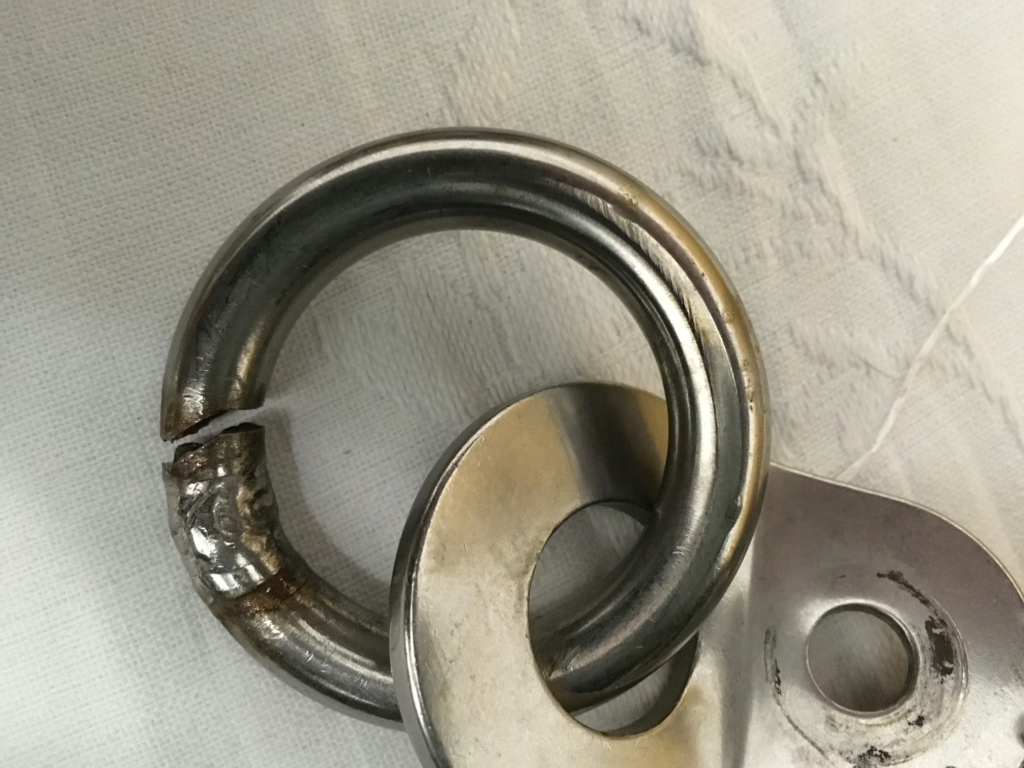
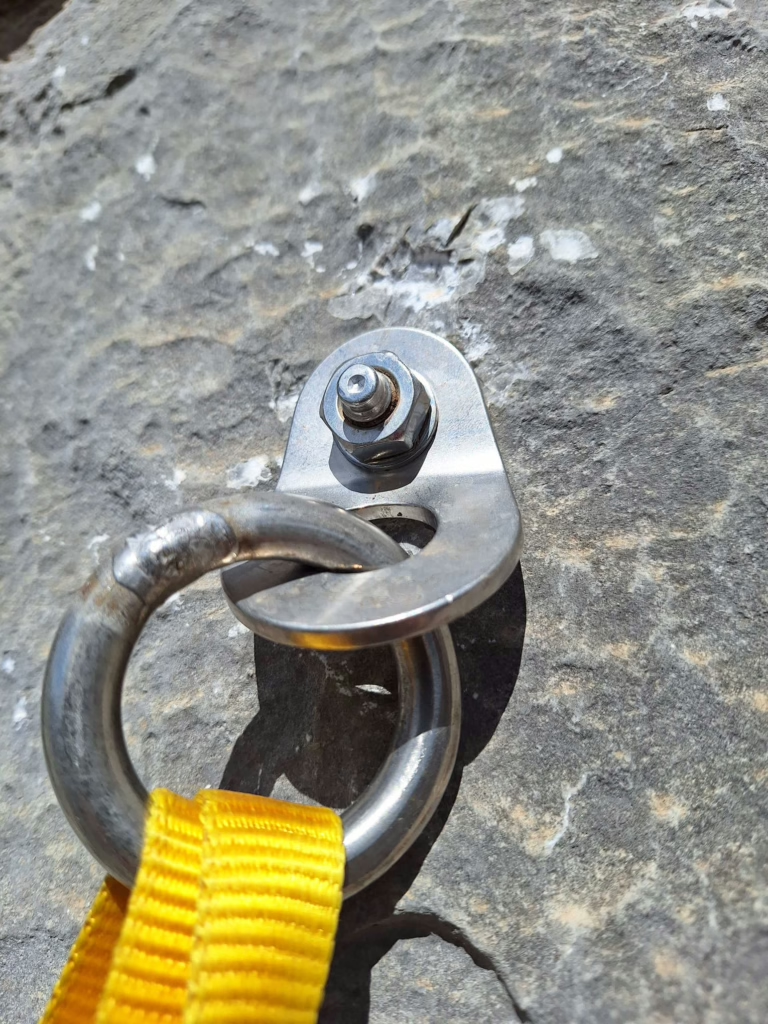
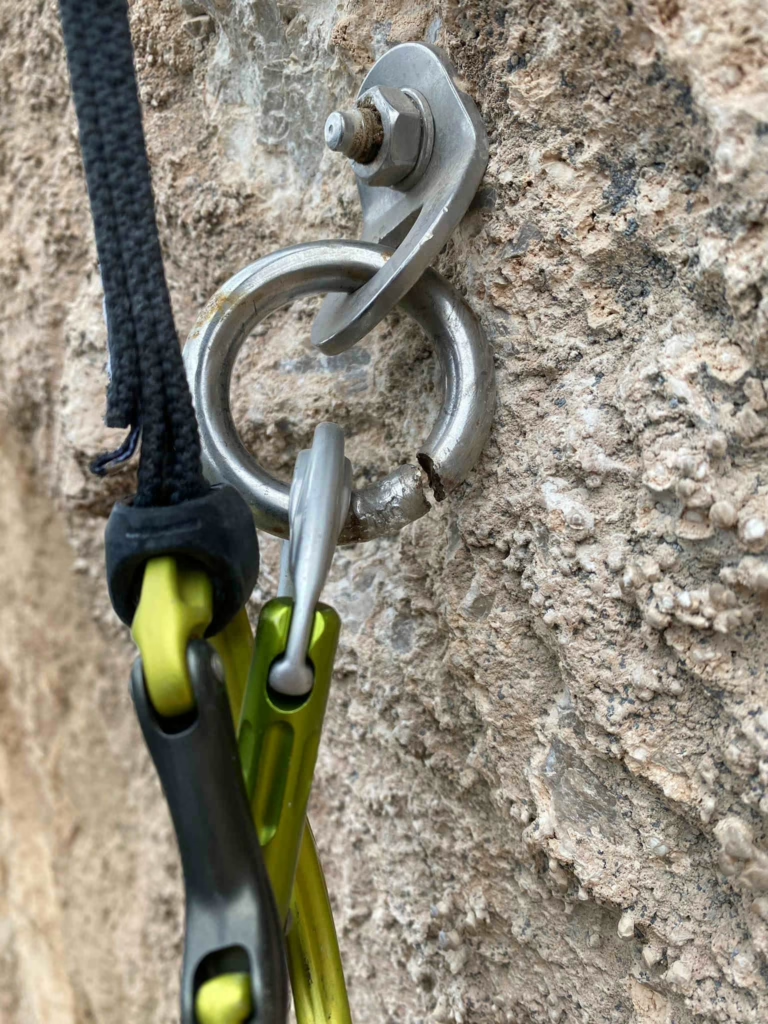
A propos d’inox
L’inox A4 316 est du 304 avec une teneur en chrome plus élevée et surtout 2 à 2.5 % de molybdène en plus pour augmenter la résistance à la corrosion. L’inox A4 316L est du 316 avec une teneur nettement plus faible en carbone, pour améliorer la résistance à la corrosion de la soudure. On le dit souvent : la soudure est le point délicat d’une boucle (cet aspect est identique pour toutes soudures). Mais les spécialistes précisent que si le travail est fait selon les règles, la soudure est aussi solide que le reste de la pièce. Ils soulignent même que cet inox A4 316L peut-être soudé sans aucun problème par la plupart des procédés et que la résistance à la corrosion n’est pas affectée par le soudage !
Les inox HCR 904L, de qualité supérieure, offrent des performances équivalentes à celles du titane du point de vue de la corrosion, avec en plus la dureté de l’acier, mais ils sont très chers.
Il existe d’autres matériaux, y compris des bons marchés, qui résistent également très bien aux agressivités. C’est notamment le cas des broches galvanisées dite au feu, posées il y a 25 ans en bord de mer, aux Calanques, voire 40 ans comme à Buoux, qui sont toujours sans corrosion. On peut trouver des spits galvanisés mais pas au niveau industriel.
A propos de la corrosion galvanique
Comme déjà vu elle se produit entre deux métaux différents en contact d’un film d’eau (l’humidité) qui contient des sels ou d’autres substances solubles dans l’eau, que l’on retrouve dans l’air marin ou pollué. Cette corrosion varie donc beaucoup selon l’environnement. Ainsi sur le continent, où l’eau et l’air en altitude sont en principe pures. il n’y a pas (ou très peu) de problèmes de corrosion galvanique, mais l’humidité de certains endroits (flancs nord) entraîne une rouille de surface du fer. Par contre, à proximité des zones urbaines ou industrielles et des bords de mer, il ne faut absolument pas assembler des métaux différents sinon la corrosion galvanique crée des dégâts.
Citons l’exemple peu connu du site de Ciampino, proche de l’aéroport dans la banlieue de Rome, où la pollution a entraîné une corrosion rapide qui a eu raison des tampons en fer sur lesquels étaient fixés des plaquettes inox A4 316L : les tiges ont facilement cassés après deux ans seulement !
Le titane
Il résiste particulièrement bien à la corrosion, mieux que les inox, mais il est beaucoup plus onéreux, même si ces dernières années son prix baisse. Le titane et les inox HCR sont les plus adaptés pour les environnements les plus agressifs. Tout comme les aciers, le titane présente des qualités très variables liées à son prix de vente.
A savoir : suite au frottement des cordes mais aussi à cause des mouvements des dégaines dans l’œil des plaquettes ou des broches (rappelons ici l’allongement des trous par les mousquetons de celles en anticorodal) le titane s’use plus rapidement que l’acier. Le titane est plus léger que l’acier mais selon sa qualité il peut être cassant. Et quelle sera la fiabilité des soudures de boucle en titane ? Aura-t-il été suffisamment testé dans le temps et sur le terrain pour l’escalade11 ? Faut-il équiper avec un produit beaucoup plus cher, pour lequel on annonce une durée de vie de cinquante à cent ans, alors que les voies souvent patinées en quelques années sont délaissées et que le matériel évolue ? Obtenu essentiellement par extraction de minerais bruts via des procédés énergivores le titane a un impact environnemental plus élevé que l’acier. On le voit, son usage est encore lié à diverses questions même si ses qualités face à la corrosion peuvent potentiellement compenser une partie du coût initial avec une durée de vie supérieure.
Le sulfure
Avec le risque d’une présence de sulfure, donc de corrosion localisée, il faut équiper les secteurs concernés avec les meilleurs inox tel que le HCR 904L ou le titane, bien que selon les tests du Professeur Santamaria des spits en inox A4 316L ont très bien résisté au sulfure de la Grotta dell’Arenauta (déjà évoquée ci-dessus) et ce pendant quinze ans.
La présence de sulfure peut entraîner une corrosion très agressive due aux bactéries sulfurogènes (sulfate reducing bacteria = SRB). Elle se produit plutôt dans des régions volcaniques ou ex volcaniques. Le net fournit des renseignements généraux au sujet de tels endroits, mais pour plus de précisions, il faut s’informer auprès de géologues spécialisés dans ce domaine. On peut également effectuer un test pour détecter sa présence (on trouve les explications à ce sujet sur le site de l’UIAA). Simple et peu coûteux, il est reconnu scientifiquement, mais il reste réservé à des organismes ou à des associations disposant de personnes qualifiées. Cependant il n’est pas infaillible, il est toujours possible qu’il ne découvre pas une zone ou une veine contenant du sulfure, si bien que l’on n’a pas de certitude absolue sur la présence ou non de sulfure… En 2022, Daniele Arena a présenté la méthode employée lors des premiers tests effectués à San Vito lo Capo, Italie.
Que faire désormais ?
Malheureusement, il faut se rendre à l’évidence : on ne peut plus simplement croire certains fabricants sur parole lorsqu’ils affirment que l’inox est de qualité et que les normes techniques ou de l’UIAA sont respectées. Et tant qu’ils affirmeront que les problèmes proviennent de la CSC (ou d’une mauvaise pose ou encore de la présence de sulfure dans la roche) et qu’ils n’admettront pas que leur matériel puisse présenter des défauts, les grimpeurs risqueront des accidents qui seraient évitables. Devant un tel déni, il faudrait multiplier les contrôles et les analyses de cet équipement, en particulier en présence de pièces corrodées prématurément. Toutefois, le recours à des expertises officielles coûte cher, et ce n’est pas l’équipeur qui peut en avancer les frais (plusieurs milliers d’euros). Seules des organisations faîtières (Fédérations, UIAA, Clubs Alpins, UIAGM…) pourraient faire effectuer de tels examens car il en va de la vie de leurs membres et de tous les pratiquants. Il faudrait surtout que l’UIAA12 opte pour des règles et des contrôles beaucoup plus stricts, de façon à garantir la qualité que les entreprises doivent absolument respecter. Elle devrait aussi se montrer plus exigeante quant à l’usage abusif de son nom, lorsque l’un d’eux se prévaut à tort du respect des normes UIAA.
Les fabricants
En présence de défauts avérés de leur matériel sur les parois, le fabricant concerné devrait venir sans délai sur place pour comprendre le problème, puis informer objectivement tous les intéressés et, à tout le moins, pour les anomalies survenues pendant la durée de la garantie légale, prendre entièrement en charge le remplacement des pièces non conformes. Ainsi, le constructeur des boucles mises en cause ci-dessus a promis à la municipalité de Leonidio de changer lui-même tout son matériel défectueux13 (ce qui n’a pas été fait après un an… et avec le risque de corrosion galvanique il faudrait changer tous les tampons) et aussi remplacer celui à l’étranger en prenant à sa charge les frais d’acheminement. On doit saluer cet engagement, en espérant qu’il sera tenu.
Les entreprises devraient renforcer le contrôle des matériaux dès l’entrée dans leurs usines pour s’assurer d’utiliser la bonne qualité ainsi que le suivi de tout le processus de fabrication et cesser le mélange de différents alliages. A noter que l’on pourrait limiter ce risque si tous les fabricants s’unissaient pour commander ensemble le même inox A4 316L de qualité certifiée qui doit être identique pour chacune des pièces. Si le type d’inox n’est en réalité pas celui qui est indiqué, il s’agit d’une pratique commerciale trompeuse.
Les fabricants devraient être en mesure d’offrir de meilleures garanties quant à la durée de vie de leurs produits : dix ans en conditions normales de vieillissement serait un minimum. Certains contrats dans l’industrie imposent une durée des matériaux, dont les tampons, jusqu’à vingt-cinq ans. Les entreprises qui parviendraient à offrir de telles garanties auraient un argument de vente décisif pour leurs produits.
Les indications sur les plaquettes (nom de l’entreprise, résistance, type de métal, etc.) pourraient être unifiées et simplifiées selon une norme qui préciserait clairement le type d’acier garanti. Mieux : que chaque pièce prévue pour l’équipement sur les parois soit identifiable sur le plan international avec un même logo simple et visible tel que AE (alpinisme, escalade)… Notons que les inscriptions au laser de certains disparaissent avec le temps ; il serait donc souhaitable que seul un marquage durable soit effectué.
Les équipeurs
De leur côté, ils doivent aussi respecter les meilleures pratiques. Signalons l’erreur courante des équipeurs : le mélange de deux matériaux tel qu’un tampon en fer et une plaquette en inox (ou l’inverse, voire, extrêmement rarement, avec du matériel pas adapté) qui est à éviter. Un test de base, certes faillible, peut néanmoins fournir un premier indice sur la présence d’inox A4 316L : l’aimant ne l’attire pas, le fer oui.
Si le spit est plus rapidement posé qu’une broche, il nécessite tout de même de maîtriser parfaitement divers paramètres bien connus (qualité du rocher, diamètre et profondeur du trou…). Face aux corrosions possibles, l’équipeur doit également veiller à :
- ne pas enfoncer un tampon inox avec un marteau en acier (pour éviter la corrosion par piqûre),
- ne pas ajouter d’autres matériaux (ni joint en caoutchouc, ni isolation, ni surplus de graisse…),
- ne pas laisser longtemps des dégaines en place (à cause du risque de corrosion galvanique),
- éviter les environnements trop agressifs (pollution intense, air salin humide, sulfure…), ainsi que :
- bien serrer la plaquette sur une surface de rocher la plus lisse possible (zone qu’il faut souvent aplanir à coups de marteau pour éviter qu’elle bouge plus tard),
- respecter le couple de serrage de l’écrou au tampon14 (pour éviter le cisaillement),
- respecter scrupuleusement d’autres directives qui pourraient être édictées.
Relais à deux boucles sans chaînes
Les équipeurs devraient privilégier le relais à deux spits avec boucles non reliées car ils sont moins chers, moins gourmands en énergie et en matériaux donc plus économiques, y compris pour l’environnement. Ils sont également plus solides, plus simples à fabriquer, à poser et à remplacer, et leur durée de vie en est prolongée. On peut remplacer les deux boucles par deux gros maillons, de même qualité que les deux plaquettes, mais celui du haut va s’user plus vite qu’une boucle suite aux moulinettes ou rappels successifs. Certes ces relais exigent de s’assurer toujours aux deux points ou de passer la corde dans les deux boucles pour mouliner ou pour le rappel.
Pour augmenter la sécurité de manière notable sans surcoûts démesuré, on peut préconiser lors de rééquipements l’emploi de spits M12.
Dans tout les cas les grimpeurs devraient d’abord effectuer les moulinettes sur leurs propres mousquetons puis utiliser en dernier lieu le matériel en place. Pour les voies les plus classiques l’ajout de maillons aux boucles des relais permet une fois usés de les changer facilement tout en limitant les frais d’équipement.
Que faire en présence de matériel défectueux ?
Les personnes qui ont des incidents avec des spits ou qui voient du matériel défectueux peuvent les annoncer aux équipeurs, aux grimpeurs et aux clubs locaux ainsi que sur le formulaire en ligne de l’UIAA : https://theuiaa.typeform.com/to/rlBZyc.
De son côté, le Professeur Santamaria est à disposition pour faire des tests du matériel d’ancrage.
Conclusion
Ces corrosions connues depuis longtemps peuvent donner une impression d’impunité et d’impuissance d’autant plus que l’on constate, en 2025, qu’une partie de l’équipement sur certaines parois n’est toujours pas fiable ! Comme déjà dit plus haut, les fabricants, les responsables et ceux qui délivrent les normes, tels que l’UIAA, doivent être beaucoup plus vigilants afin d’obtenir enfin une qualité irréprochable des produits. Au risque d’encore le répéter, les équipeurs doivent aussi redoubler d’attention afin de mettre en place l’équipement le plus sûr.
Un dernier point rassurant : l’essentiel de ce matériel en place est heureusement fiable. De qualité, répondant aux normes et aux indications données, il se comporte parfaitement. D’ailleurs les deux éminents Professeurs Ulderico Santamaria et David Reeves15, n’ont jamais trouvé un inox A4 316L fabriqué correctement qui aurait été affecté par de la corrosion localisée. Aucun à ce jour depuis douze ou quinze ans !
Remerciements
Daniele Arena, Ivan Cherpillod, François Dupont, Federico D’Isep, Bruno Fara, Renée Guerin, Lionel Kiener, Enrico Mazzoli, Jean-Michel Pauchard, Emanuele di Pellizzari, Stéphane Rouvinez, Ulderico Santamaria, Aris Theodoropoulos, ainsi que Daidalea Associazione Culturale et Carmela Malomo.
Bibliographie
- G. Di Caprio, Gli acciai inossidabili, 3° ed., Hoepli, 1997.
- V. Boneschi, M. Boniardi, Gli acciai inox e la resistenza alla corrosione, publié par da Lamera, avril 2008. Rédigé sur la base du rapport présenté au cours « Failure Amalysis and prevention » organisé par le Politecnico di Milano Campus Bovisa Nord, Milano 19-22 Febbraio 2008[2] F. Capelli, Cosa sono gli acciai inox, “Tecnologie Alimentari” n.3, mai 1994.
- Stainless Steel, ASM Specially handbook, 1994.
- J. W. Fielder, D.R. Johns, Proc. Conf. UK Corrosion ’89, Blackpool, 1989.
- M. Boniardi, C. Anchisi, V. Boneschi, Resistenza alla corrosione e metodi di indagine degli acciai inossidabili, séminaire Centro inox-IMOA “Gli acciai inossidabili duplex”, Milano 29 mai, 2001.
- Decapaggio e passivazione, par M. Boniardi, V. Boneschi, extrait de Trattamenti e Finiture, juillet 2005. www.meccanicanews.com
- Pickling and passivating stainless steel, di Euro Inox 2007
- Fenomeni di danneggiamento dei materiali metallici dovuti all’esercizio, Boniardi, Casaroli, Tagliabue.
- Problèmes de corrosion des spits, Groupe de Haute Montagne de Lausanne,
- en français https://www.ghmlausanne.com/_files/ugd/9299e4_b39154777f2f4eab8f23b54664bdbf0b.pdf
- en anglais https://www.ghmlausanne.com/_files/ugd/9299e4_997b2ea7a7c84eb4b70f6be5b79a60ad.pdf
- Lien de l’article publié en Italie
- Lien de l’article avec l’interview de C. Malomo par Montagna.TV
- Klettern 8/2024, en allemand : Sichere Sache ? C. Remy.
- Passion Montagne, section des Diablerets du Club Alpin Suisse, 4-2025 et site internet de la section des Diablerets du Club Alpin Suisse,
- La corrosion a de nombreuses origines, s’il est difficile d’établir la plus dangereuse, c’est toujours le stress qui accélère le processus et aggrave les conséquences. De manière générale la CSC regroupe toute corrosion que l’on ne parvient pas à identifier où à laquelle contribuent plusieurs causes. ↩︎
- Pour l’équipement de l’escalade, l’inox A4 316L est celui qui a été retenu comme étant le meilleur rapport qualité-prix pour la très grande majorité des sites d’escalade y compris en bord de mer. ↩︎
- Le meilleur marché mais il rouille en cas d’humidité. Si ce n’est que sur la surface les qualités de l’acier changent peu mais comment en être certain ? Précisons que des tampons en simple acier placés dans des flancs nord et humides en Suisse ont été retrouvés après plusieurs années en mauvais état. Sans connaître le solde de leur résistance, les remplacer par de l’inox était l’évidence. ↩︎
- Plus coûteux, les inox sont des aciers alliés. ↩︎
- Seront également utilisés, mais dans une moindre mesure, du M12 et des broches collées. ↩︎
- Elle se produit lors du contact de deux métaux différents dans un environnement humide, exemples : fer et aluminium, inox et titane, voire même entre deux inox différents (voir plus loin le mot sur cette corrosion) ! ↩︎
- Lire l’article de Bruno Fara sur le sujet publié dans la revue Roc info de l’Escalade Club de l’Isère (ECI), no 50, en 2019 qui ne mâche pas ses mots à l’égard des fonctionnaires et des institutions (FFME et UIAA, notamment). Hélas, depuis cela n’a pas beaucoup changé. ↩︎
- Imaginer la rupture de deux tampons à un relais ou à celui d’un voie de plusieurs longueurs… ↩︎
- Issu de l’UIAA 123 standard update about corrosion and stress cracking failure of climbing anchors 2020. ↩︎
- L’expertise détaille clairement les tests effectués, le laboratoire a conservé toutes les pièces examinées afin que, si nécessaire, les analyses puissent être répétées par d’autres organismes autorisés à effectuer des analyses ayant valeur de preuve. ↩︎
- Depuis 2009, l’entreprise anglaise Titan Climbing est la première à fabriquer des broches en titane qu’il faut coller. Les broches de 12 mm de diamètre, ou plus, en inox ou en titane présentent une solidité supérieure au spit, pour autant qu’elles soient bien posées. Le problème d’une broche est sa mise en place : elle demande plus de temps et de soin que le spit. Hélas, des broches sont parfois mal fixées, ce qui arrive plus souvent qu’avec des spits. À noter que des spits en titane existent mais certains se sont cassés facilement… ↩︎
- Sur le même sujet, le site de l’UIAA donne de plus amples informations. ↩︎
- Les plaquettes analysées qui sont non conformes étaient fixées sur des tampons inox A4 316L ! Ce qui va engendrer de la corrosion galvanique ! Hélas, de tels assemblages ont été posés sur de nombreux sites et voies en Grèce et ailleurs. ↩︎
- Une clé dynamométrique permet un serrage ad hoc et fiable d’un écrou sur un tampon. Pour un M10 en inox A4 316 L, il est de 25 Nm. ↩︎
- A lire l’excellente documentation du Professeur Reeves sur la corrosion que l’on retrouve sur le net : https://craqchemistry.com/2010/1’/05austenite-stability-are-we-missing-something-here/ et https://cragchemistry.com/wp-content/uploads/2020/04/UIAA-Sulphate-Sample-Kit.pdf ↩︎